KCam, EMC2, Mach3, TurboCNC,and other CNC related software links.
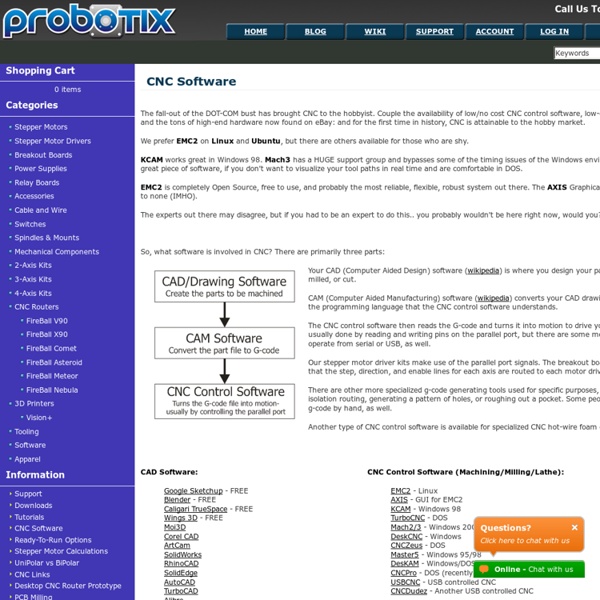
The fall-out of the DOT-COM bust has brought CNC to the hobbyist. Couple the availability of low/no cost CNC control software, low-cost integrated circuitry, and the tons of high-end hardware now found on eBay: and for the first time in history, CNC is attainable to the hobby market. We prefer EMC2 on Linux and Ubuntu, but there are others available for those who are shy. KCAM works great in Windows 98. Mach3 has a HUGE support group and bypasses some of the timing issues of the Windows environment. EMC2 is completely Open Source, free to use, and probably the most reliable, flexible, robust system out there. The experts out there may disagree, but if you had to be an expert to do this.. you probably wouldn't be here right now, would you? So, what software is involved in CNC? Your CAD (Computer Aided Design) software (wikipedia) is where you design your parts to be routed, lathed, milled, or cut. Our stepper motor driver kits make use of the parallel port signals.
Stepper Quickstart
Gather information on steps and gearing. The result of this is steps per user unit which is used for SCALE in the .ini file. Steps per revolution - is how many stepper-motor-steps it takes to turn the stepper motor one revolution. Typical is 200. Micro Steps - is how many steps the drive needs to move the stepper motor one full step. If microstepping is not used, this number will be 1. The net result you’re looking for is how many CNC-output-steps it takes to move one user unit (inches or mm). Example 1. Stepper = 200 steps per revolution Drive = 10 micro steps per step Motor Teeth = 20 Leadscrew Teeth = 40 Leadscrew Pitch = 0.2000 inches per turn From the above information, the leadscrew moves 0.200 inches per turn. - The motor turns 2.000 times per 1 leadscrew turn. - The drive takes 10 microstep inputs to make the stepper step once. - The drive needs 2000 steps to turn the stepper one revolution. Example 2.
Stepper motors
Intro Stepper motors enable precise positioning without needing sensors to measure motor position. Each pulse to a stepper motor turns its shaft one step which for many steppers is 3.6 degrees. One hundered pulses will turn a 3.6 degree stepper exactly one revolution. Finding a stepper motor Stepper motors are available new, from surplus houses, or can be pulled from old electronic equipment such as floppy drives. Look for "unipolar" or "4-coil" or "4-phase" motor (they all mean the same thing) with 5 or 6 or 8 wires. Key specs are operating voltage (12V is convenient for robotics projects), and either coil current or coil resistance (given one spec you can get the other from V=IR). If you are pulling a motor from an old floppy drive, look for a flat motor with five or six leads. Identifying stepper motors If you are staring at a pile of stepper motors in a surplus shop, or have pulled one out of used equipment, here's how you can determine what you have. Next, read the label on the side.
Related:
Related: