Faberdashery Ltd. - 3D Printing Things
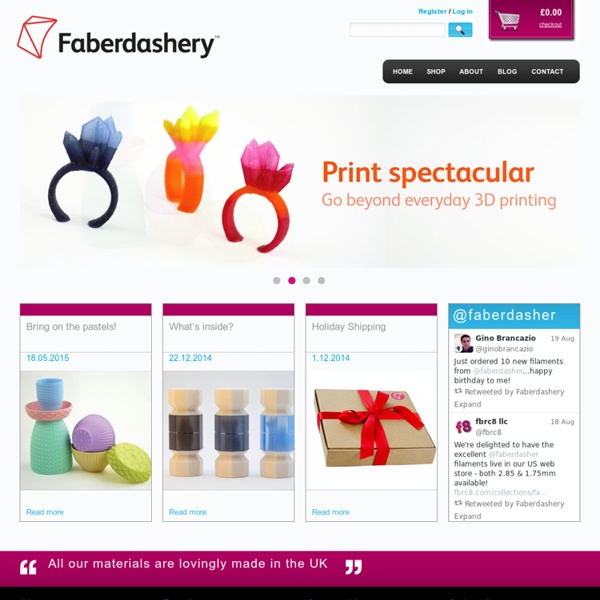
Drawing Machine
So I've built my first CNC bot, a drawing machine. Because that wasn't quite difficult enough on its own I decided to make one that uses polar coordinates. That is, one with an arm that can spin on a base, and move in and out relative to the centre. It gives you a very large drawing surface with a minimum of moving parts compared to a standard x,y Cartesian plotter. I was inspired by similar projects online, like the eggbot and the polargraph which uses a dual polar coordinates system; mines a single. The general setup is a pair of nema-17 motors, being run by dSpin motor drivers. One important note, if you use a solenoid for the pen lifter you need a really good diode to drain the current when you depower it otherwise the back EMF does bad things. Here are some videos, first the movement test: First drawing: As for the build. Once I got it glued up and assembled using every clamp in the shop, plus an anvil, blower, forge, and anything else heavy on top.
MakerSlide Open Source Linear Bearing System by Barton Dring
Sorry about the lame video. I am not very good at that kind of thing, but I am good at designing and building CNC and digital fabrication equipment. I have a great idea for a linear bearing system. I hope you will take the time to hear/read my pitch and consider donating to this project. A big cost driver and fabrication hurdle for home built CNC equipment is the linear bearing system. Commercial systems are expensive. There are hundreds of DIY methods. My proposal is to create a standardized replacement for a lot of those solutions. I know there are commercial system similar to this. My goal is a sell price of $0.10 per centimeter. MakerShip Program This is available to any level supporter.
Related:
Related: