Six Sigma - What is Six Sigma?
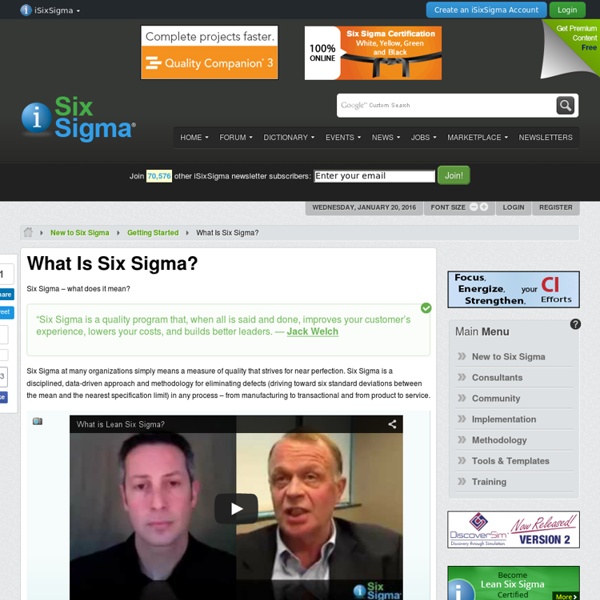
Six Sigma – what does it mean? “Six Sigma is a quality program that, when all is said and done, improves your customer’s experience, lowers your costs, and builds better leaders. — Jack Welch Six Sigma at many organizations simply means a measure of quality that strives for near perfection. Six Sigma is a disciplined, data-driven approach and methodology for eliminating defects (driving toward six standard deviations between the mean and the nearest specification limit) in any process – from manufacturing to transactional and from product to service. The statistical representation of Six Sigma describes quantitatively how a process is performing. To achieve Six Sigma, a process must not produce more than 3.4 defects per million opportunities. The fundamental objective of the Six Sigma methodology is the implementation of a measurement-based strategy that focuses on process improvement and variation reduction through the application of Six Sigma improvement projects.
White Papers: Six Sigma deployment, Six Sigma strategies, LEAN M
Excellence in Healthcare with Lean Six Sigma This 9-page whitepaper discusses the application of Lean Six Sigma in the Healthcare industry. The roles Lean Six Sigma can play in Healtcare as well as some success stories are presented. Download now History of Six Sigma This short 10-slide powerpoint provides an overview of the history of Six Sigma, tracing its roots from the "normal curve" to GE's global promotion and beyond. Download now Changing the Compliance Formula .. and Improving Competitiveness An executive brief that discusses the importance of basic process management and improvement discipline for effectively and efficiently managing compliance requirements and the risks associated with those requriements. Download now Design Basics - QFD Overview A high-level overview of QFD and how it can be applied to drive good, customer-focused designs by aligning technical / product / service requirements with real customer requirements. Download now VOC Deployment and Maturity Model Download now
Lean Sigma Search - Avery Point Group - Executive Search & Recru
TRACtion Lean Six Sigma Project Tracking and Management
TRACtion - A Tool for the Entire Team TRACtion pricing is a function of several factors, the foremost of which is level of usage. We believe that ALL team members should be empowered to access and view project data, status updates, summaries, and project tools on an as-needed basis. To encourage deployments to involve all their team members in project management, we do not charge for licensed usage by team members (e.g., non-team leaders, process owners). We only charge annually for "Power Users" - our term for the group of your practitioners who will gain the most value from TRACtion. Power Users are the heaviest users of TRACtion's features (e.g., Team Leaders, Champions, and Financial Auditors). How Is TRACtion Priced? TRACtion is licensed per year and is based on the number of Power Users in your company. Example If you have 10 Team Leaders (Black or Green Belts) and 2 Champions, you would need to license TRACtion for 12 Power Users. Contact Us to Discuss Pricing
Related:
Related: